In an industry as fast-paced and innovative as automotive, it’s evolved beyond measuring with heavy, bulky traditional fixtures. Yet many automotive manufacturers are still struggling with these tools and the accompanying challenges: repeatedly measuring for a complete quality check, involving multiple team members for a one-person job, manufacturing new fixtures for every design iteration, and more. At RapidFit, we’ve combined lightweight materials with 3D printing to provide fixtures that simplify the measuring process in the following ways.
1. Handle lightweight fixtures with ease
Our fixtures combine carbon components with 3D-printed parts to make them up to 90% lighter than conventional alternatives. With a lighter fixture, you can drastically cut down on the time spent attaching parts and running scans during the measurement process. Plus, setting up those heavy measuring fixtures typically requires multiple people and increases the risk of injury. Just one person can quickly and safely set up and scan the parts with our measurement fixtures.
On top of measuring the part itself, these tools must also conduct nominal simulations of adjacent vehicle components. 3D printing offers benefits here as well. The technology’s additive nature means we get to work with design freedom that other manufacturing methods can’t accommodate, so we print these parts with internal honeycomb structures that drastically reduce the overall weight.
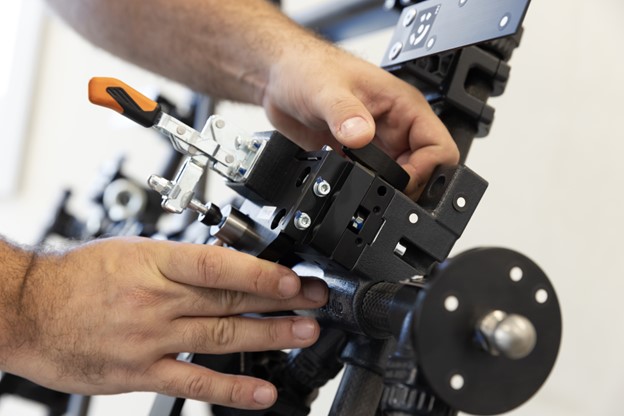
2. One solution for your plastic, sheet metal, and carbon parts
If hearing ‘lightweight fixture’ sets off alarm bells because you don’t imagine it could handle assembled parts (which can be heavy and complex), you’ll be happy to know that’s not the case with our fixtures. We tailor the tool according to your part and leverage different manufacturing methods depending on the weight requirements. Thanks to our extensive knowledge in design, materials engineering, and manufacturing, our team captures the perfect balance in fixture design to accommodate your needs.
3. Use fewer fixtures for your project
Every part requires a unique measuring fixture, right? That’s not the case with 3D printing. Our fixtures are modular — they include 3D-printed clips that can be easily assembled and removed depending on which part is being measured. Let’s take car doors, for example. With one fixture, you check all four car doors as long as they’re all manufactured in the same location. Just attach the tailor-made 3D-printed components to the fixture when needed. We have one customer who only needed 34 fixtures to measure 58 parts. For you, that could mean spending way less on manufacturing and shipment.
4. No more excessive rescanning
The lightweight structures don’t only improve weight; they also reduce the surface area around your part. The bulk from conventional fixtures prohibits you from having direct access to the entire part, requiring multiple rescans to cover the whole surface. Our slim fixtures take up much less space and make scanning easier and faster.
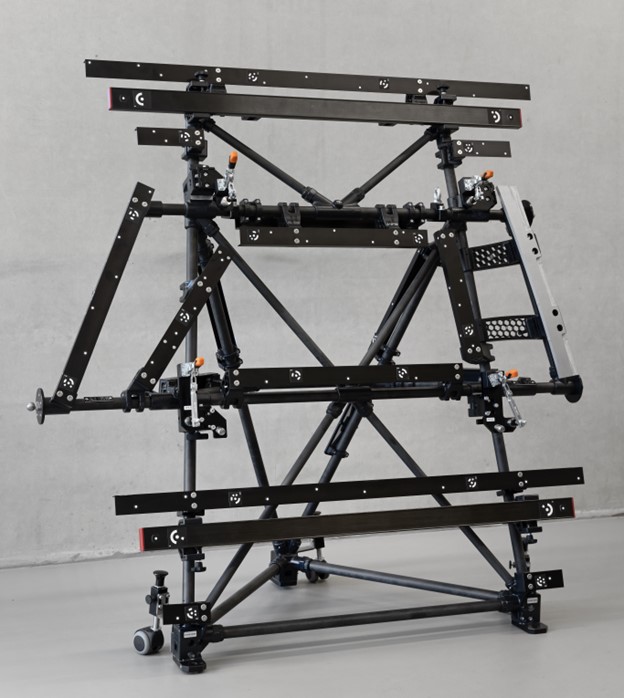
5. Iterate with ease
Yet another advantage of 3D printing is its digital nature. Whereas other fixtures need to be sent back to the manufacturer for any design change to your vehicle, we have all of the necessary files available on demand and can fine-tune the design, print the part, and ship it to you in just a few days. You’ll save time, costs, and the headache of restarting the manufacturing process from scratch each time.
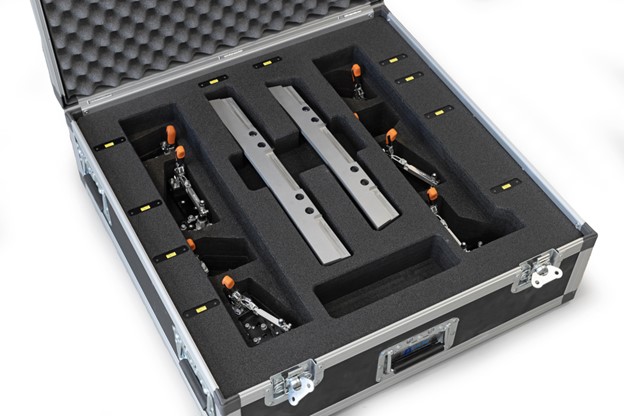