Why does the automotive industry choose RapidFit? We sat down with Managing Director Bart Wilberts to ask him all about the current state of the automotive industry, the benefits AM brings to tooling, and what the future holds.
Hi Bart. Would you please give us a brief description of RapidFit and what we do for those who don't know?
RapidFit is a daughter company of Materialise, a company here in Belgium that has specialized in 3D printing for more than 30 years. We design and manufacture fixtures and cubes for the automotive industry using advanced technology, such as additive manufacturing. Once the design of a vehicle is set, our customers have to start developing the actual body panels and parts within certain strict specifications. In this phase, our cubes and fixtures are mostly used for quality control of the vehicle’s inner and outer body panel, including headlamps and rear lamps.
Next to that, we also have some business in lightweight tools used on the production line. Being lightweight, they are more ergonomic for the workers to use. For example, imagine you want to position the templates on an SUV. When it’s made of aluminum, that tool weighs between 28 and 30 kilos. When we make it in carbon fiber, using 3D-printed parts, we can reduce the weight to 11 or 12 kilos, so by more than 50%. Those are the two main areas where we serve the automotive industry.
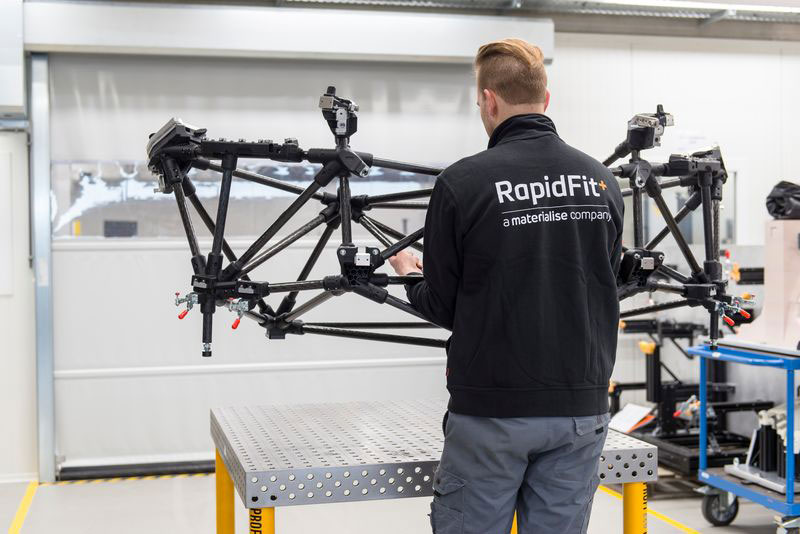
You mentioned weight reduction and improved ergonomics. Would you say those are the main benefits of working with RapidFit?
Well, apart from being more ergonomic and lightweight, it all starts with a small and high-quality team that understands the needs of our customers very well. We also have certain applications that allow us to provide a more cost-efficient proposal. And certainly, one of the biggest advantages of using additive manufacturing in our production is that we can deliver full fixtures and cubes faster than we could with any traditional technology, such as milling. As far as weight goes, it's not only about being lightweight, which is important. Sometimes our customers set a target weight for certain fixtures. So, for example, they ask us to simulate a headlamp that should weigh around, you know, two and a half kilograms. With additive manufacturing, we can come really close or even hit the target weight for that kind of item. With traditional technology, it's a lot more difficult to approach the actual weight of the finished part.
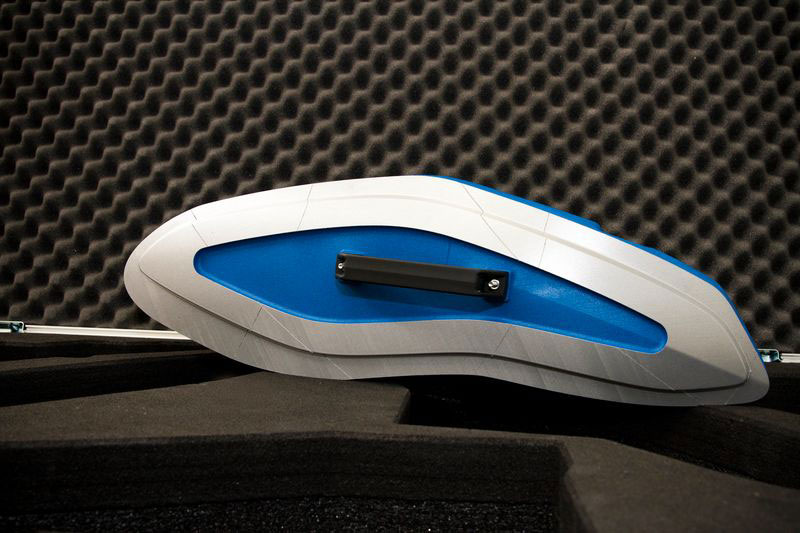
Efficiency has always been important in the automotive industry. How does RapidFit offer that?
We offer this in two ways.
Firstly, on a data level, we are very highly integrated with our customers. So, we store the data of what we developed for them according to the rules and regulations of the TISAX certification for the German auto industry — just one aspect of our commitment to quality. And it also means that if they want to make an order later on, they don't have to send anything back — we can design, develop, and manufacture items based on the information in our database. So, the customer can continue working with the base structure, the fixtures and cubes, they got from us two or three years ago. While they do so, we are developing the new items, and we can send them to the customer for assembly without disturbing their operations during this process. The second one is modularity — in two senses. First, we use a modular approach to build our traditional fixtures with an aluminum base plate and parts. Only at the end, when we have to simulate the actual part of the vehicle, is anything 3D printed. At the end of the lifecycle, we can recuperate all these aluminum parts and reuse them rather than having to recycle anything.
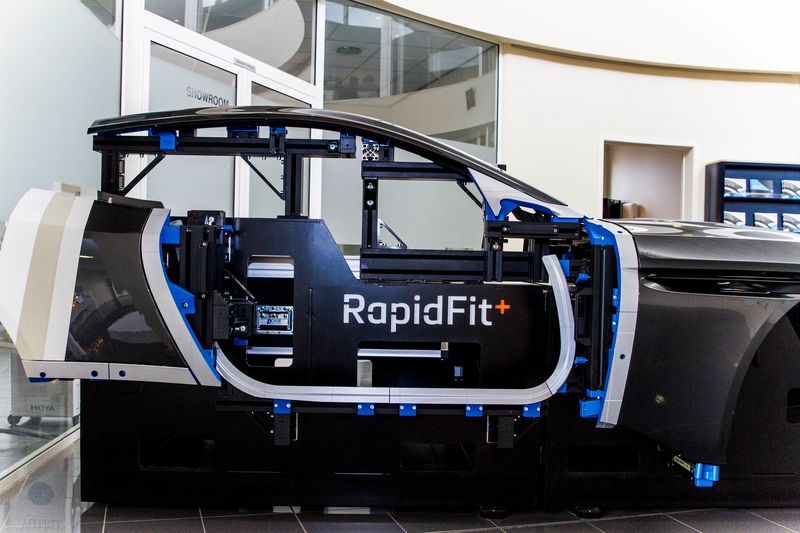
There is also modularity in our cubes, as long as the chassis of the vehicle is the same. For example, we once built a front simulation of a vehicle for one car brand, where the frame essentially simulates the chassis, and then all the body panels, the headlamps, the grille, the hood, and the fenders are simulated with 3D-printed parts (volumes). And then, a few months later, in the same factory, they started production of a second version of the same vehicle, but under a different brand. While the cube was still in use in the factory, we printed the full second version based on the same frame.
So, the customer only bought the frame once, and then two packages of volumes to simulate the front of the car. This allowed for a cost saving of 60% compared to the full development of a new vehicle. So, because of modularity, more models built on the same chassis, we have a much more cost-efficient proposal compared to our competitors.
I guess that also makes RapidFit quite a sustainable option?
It's a massive material saving because the simulation of the frame is usually an aluminum or steel structure that is really big and heavy. And obviously, as you are simulating multiple vehicles on one frame, you save a lot of material and CO2 in production.
Another example is an extreme sports vehicle, where we made a simulation of the entire body. First, the standard version, the closed version, then with some minor modifications on the same frame, we developed the convertible version and the long-tail version with the high output engine. So, you use a lot less material, and at the same time, you can simulate three different vehicle shapes on the same cube if you want.
Many businesses were hit hard by the pandemic. Has the automotive industry changed as a result of COVID 19?
Before the pandemic, the strategy was, you know, let's keep doing our big internal combustion engines. Let's keep doing the hybrids. And slowly and cautiously, let's look at what we have to do in electric vehicles. Then the pandemic hit. After the pandemic, automotive manufacturers in Europe are suddenly accelerating the launch of electric vehicles. Has it changed the automotive industry? Clearly. It's a paradigm shift. It's a big break away from the traditional approaches that they had before.
“The RapidFit technology for cubes is much more cost-efficient for electric vehicles than any of the traditional construction techniques for vehicle simulations currently on the market.”
Has this shift created more challenges for the automotive industry?
To build an electric vehicle, you need 40% fewer parts than an internal combustion vehicle. So, as a consequence of this, a lot has to change, and that investment is really costly. However, margins are under pressure with electric vehicles, meaning there's a lot of demand for suppliers to reduce costs.
How does the automotive industry do that? Can RapidFit help?
Fundamentally, by using the same platform (a combination of an engine, drivetrain, and a chassis) to build multiple vehicles, because the highest cost is in the development of a platform. For example, a major American brand announced that they want to bring their total number of platforms down from 150, where it is today, to just 19 by the time they move entirely to electric vehicles. Similarly, a German brand announced that they want to build their full lineup on three platforms by 2030. So that is dramatic. But that is where they will save costs. Once they've done that, and remembering what I told you before, we are fantastically efficient if we can have one chassis simulation. We can build any vehicle on top of this one chassis with extreme efficiency while remaining conscious of costs. So, the RapidFit technology for cubes is much more cost-efficient for electric vehicles than any of the traditional construction techniques for simulations currently on the market.